The Bullwhip Effect in Supply Chain: Causes, Impact, and Strategies to Mitigate It
Introduction
In the world of supply chain management, efficiency is paramount. However, even the most well-planned supply chains can fall victim to a phenomenon known as the ‘bullwhip effect’. This term describes how small fluctuations in demand at the consumer level can cause increasingly larger fluctuations in demand upstream in the supply chain. These distortions lead to inefficiencies, increased costs, and operational disruptions.
What is the Bullwhip Effect?
The bullwhip effect occurs when variations in consumer demand lead to exaggerated fluctuations in orders from retailers to manufacturers and suppliers. The further you move upstream in the supply chain, the larger these fluctuations become, resembling the motion of a cracking whip.
This issue is particularly common in industries with complex supply chains, such as retail, manufacturing, and e-commerce, where miscommunication, misaligned incentives, and forecasting errors create inefficiencies.
Causes of the Bullwhip Effect
Understanding the root causes of the bullwhip effect is essential for minimizing its impact. Some of the primary causes include:
1. Demand Forecasting Errors
Businesses rely on historical data to forecast demand. However, inaccuracies in these forecasts lead to over-ordering or under-ordering, exacerbating fluctuations further up the supply chain.
2. Order Batching
Companies often place bulk orders at scheduled intervals rather than ordering based on real-time demand. This approach creates artificial spikes and lulls in demand, worsening the bullwhip effect.
3. Price Fluctuations and Promotions
Temporary price cuts, promotions, and discounts encourage customers to buy in bulk, leading retailers to place large, irregular orders. Once the promotion ends, demand plummets, creating instability.
4. Lack of Communication and Coordination
Poor communication between different tiers of the supply chain results in misalignment. If retailers, wholesalers, and manufacturers do not share real-time data, each party acts independently, amplifying demand distortions.
5. Long Lead Times
Longer supply chain lead times make it difficult to respond to changes in demand efficiently. This delay forces businesses to rely on inaccurate forecasts, which can further exacerbate order variability.
Impact of the Bullwhip Effect on Businesses
The consequences of the bullwhip effect can be severe for companies across various industries. Some key impacts include:
- Excess Inventory – Businesses end up with overstocked warehouses, increasing carrying costs and reducing cash flow.
- Stockouts and Lost Sales – Overcompensation in inventory management can lead to stock shortages, resulting in unsatisfied customers and lost revenue.
- Increased Costs – Fluctuating demand results in higher production costs, expedited shipping fees, and storage expenses.
- Supplier Disruptions – Suppliers may struggle to meet erratic order patterns, leading to production inefficiencies and potential supply chain breakdowns.
- Reduced Customer Satisfaction – Delays, stockouts, or surplus inventory impact service levels and erode brand trust.
Strategies to Mitigate the Bullwhip Effect
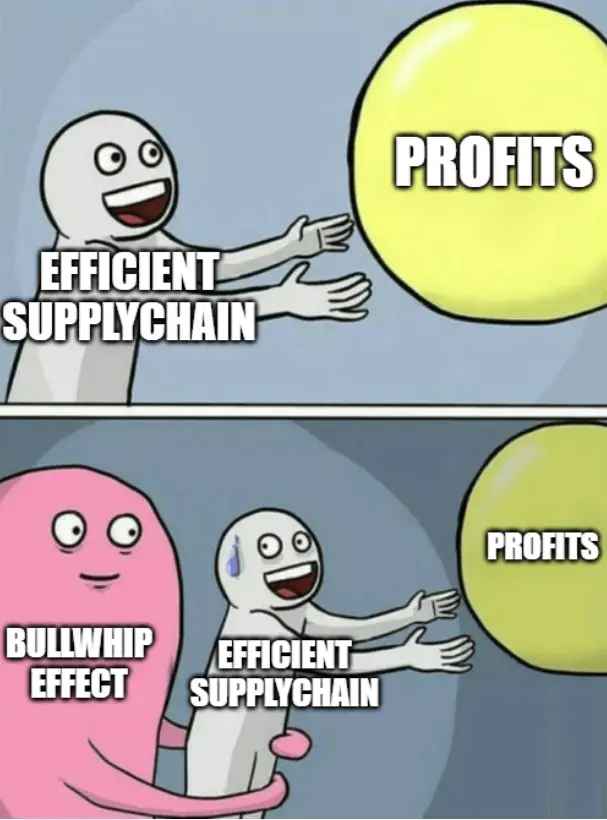
To minimize the impact of the bullwhip effect, companies can implement the following best practices:
1. Improve Demand Forecasting with Data Analytics
Leveraging AI-driven analytics and real-time data tracking can improve demand forecasting accuracy. By incorporating machine learning models, businesses can reduce reliance on historical trends and respond dynamically to market changes.
2. Enhance Communication and Collaboration
Implementing Collaborative planning, forecasting, and replenishment (CPFR) allows retailers, wholesalers, and manufacturers to share real-time data. This transparency helps in making informed supply chain decisions.
3. Adopt Just-in-Time (JIT) Inventory Management
JIT inventory management helps in maintaining optimal stock levels by reducing reliance on large batch orders. By aligning inventory replenishment closely with actual demand, businesses can smooth out order fluctuations.
4. Implement Demand Smoothing Techniques
Rather than offering deep-discount promotions, companies can adopt consistent pricing strategies and loyalty programs to encourage steady purchasing behavior and reduce demand surges.
5. Reduce Lead Times
Working closely with suppliers to shorten production and delivery lead times can improve supply chain responsiveness. Using Local suppliers, Automation, and Agile manufacturing can help in reducing delays.
6. Utilize Advanced Supply Chain Technologies
Investing in blockchain, IoT, and cloud-based ERP systems allows real-time tracking of inventory and demand changes. These technologies improve visibility, enabling more accurate forecasting and quicker response times.
Conclusion:
The bullwhip effect remains a significant challenge in supply chain management, causing inefficiencies, increased costs, and customer dissatisfaction. However, by adopting modern technologies, improving communication, and refining forecasting techniques, businesses can mitigate these disruptions and build a more resilient supply chain.
Companies that proactively address the bullwhip effect will be better equipped to handle demand fluctuations, reduce waste, and maintain a competitive edge in the market. By fostering greater transparency and agility within the supply chain, organizations can ensure long-term sustainability and efficiency.